Tungsten Carbide Wear Parts Wear Compare
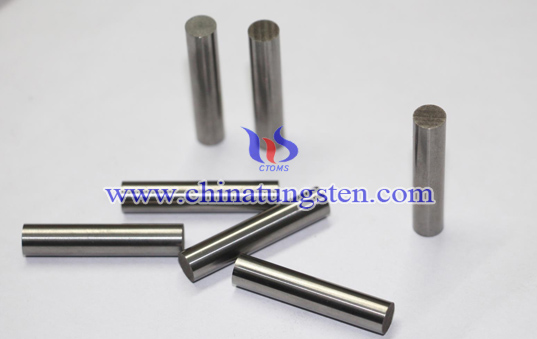
Wear and corrosion is a major cause of industrial materials and energy loss caused. WC particles having a high melting point, high hardness and good stability, tungsten carbide particles and iron-based metal wetting angle is zero, and the ceramic particles with other metals (e.g., titanium carbide, etc.) compared to the readily available, so the WC particle reinforced composite material is more and more important.
WC powder and cast tungsten carbide is tungsten metal powder as raw material, according to the carbon content requirement formulated as a mixed material was charged into a graphite boat and melted in a melting furnace and supplementary carburizing about 3000 ℃ in, casting the melt into a strip, and then The cast strip crushing, grading, made of various size range cast tungsten carbide. Cast tungsten carbide is WC and W2C eutectic, Rockwell hardness of up to 93 ~ 93. 7 HRA, its hardest component of micro hardness W2C 2 500 ~ 3 000 HV, so it has a very good abrasion resistance.
2. Sintered tungsten carbide wear parts
The tungsten carbide powder and tungsten powder in a certain ratio with the prepared mixture, briquetting, sintering, and mechanical crushing / sieved became a variety of cemented tungsten carbide powder. The actual production of the fine particles have cast tungsten carbide powder and cobalt formed mixture, and then pelletizing, sintering, mechanical disruption, manufactured in a sintered tungsten carbide. This cemented tungsten carbide and cobalt in W2C most brittle M6C phase reaction. Sintered tungsten carbide with cobalt or nickel cemented tungsten carbide particles, Rockwell hardness greater than 88 HRA, slightly lower than the cast tungsten carbide wear resistance, flexural strength 1 400 MPa, impact resistance greater than cast tungsten carbide.
Using a special process is mixed with the tungsten powder carbon black, high temperature carbonization furnace in carbonation, tungsten carbide single crystal can be obtained. This tungsten carbide hardness and toughness between cast and sintered tungsten carbide. At the same time, which is good for the iron group metal wettability. However, in the surface layer of tungsten carbide composite crystal content is not too high, otherwise prone to bridging monocrystalline tungsten phenomenon, especially laser cladding process can easily occur. This binding force between the bridge surface is weak, prone to damage under external load from there, leading to the occurrence of spalling WC, reducing wear.